Dear Ed,
Here comes what you were waiting for:
A from the scratch new design and alternative for the old style. It is a very simple design but with a team of people rather unexperienced it was a nightmare to produce it. The parts were designed by me and are cut out of stainless steel plates. Later they had to be crimped and then welded. It started with the crimping that was done by unprofessionals that crimped wrong and also used the wrong press. The 1st welder I found was not able to make a good welding and the parts became scrap. So we had to have them cut again and find a better crimper to bend them and a better welder to weld them.
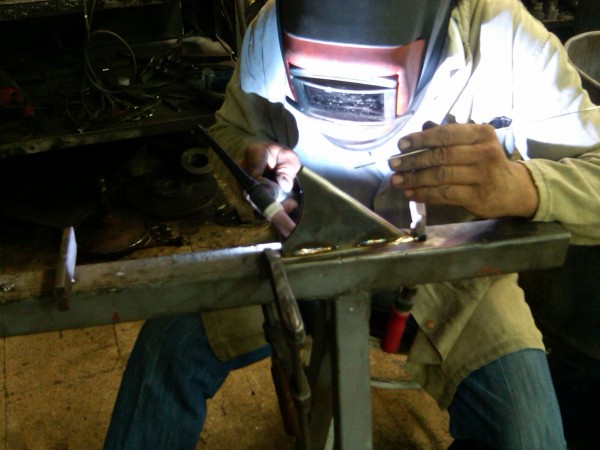
- This welder was perfect!
Besides this we had to down machine one side so that we catch an angle of +15 and - 15 degrees as our boat rounded-top. Screws had to be bought and we had to cut-in a thread to some of the holes.
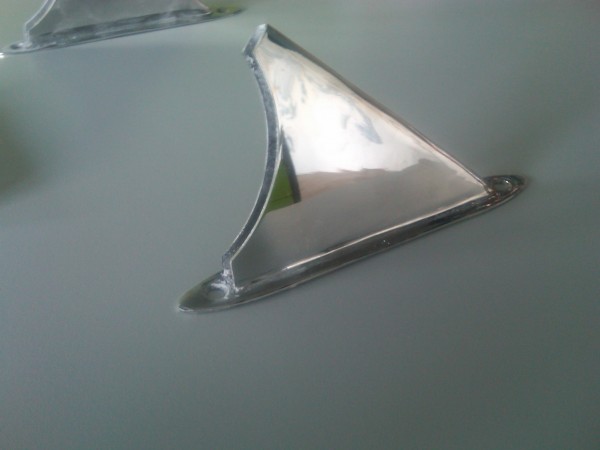
- Shark-fin design
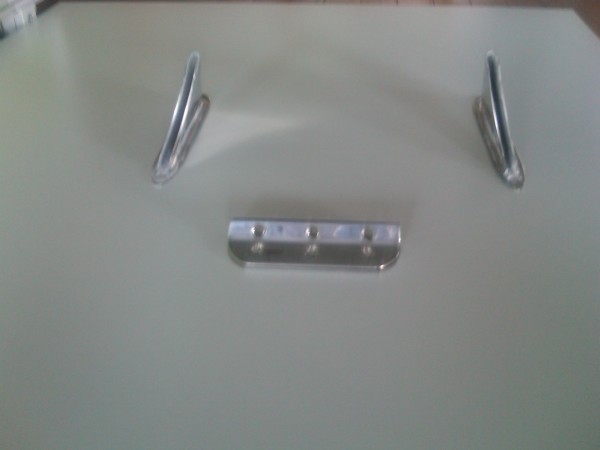
- The assembly as a set
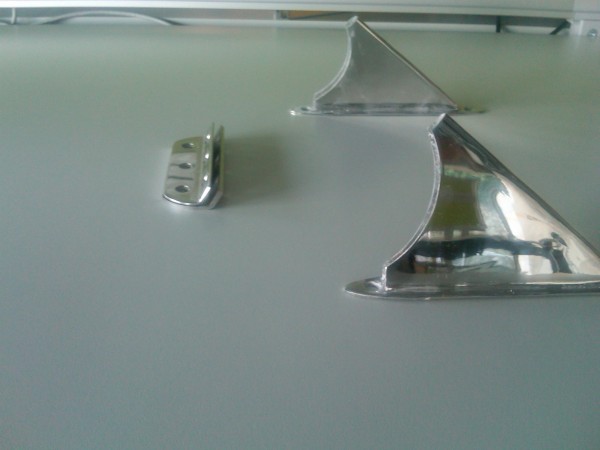
- Set from the side!
The set consists of a middle part and two side parts. Besides this there is (will be) a lower and an upper frame. The lower frame has still to be produced and we will use very thin stainless steel sheet, which we will bend in a can production machine. For the upper frame we want to use the original Volga frame profile we still have in hand, but need to bend it according to the new shape.
The middle part will be at front screwed to the deck, fix the plexiglass and hold it down, whereas the sharkfin sides will hold the sides and back, when they slide in it.
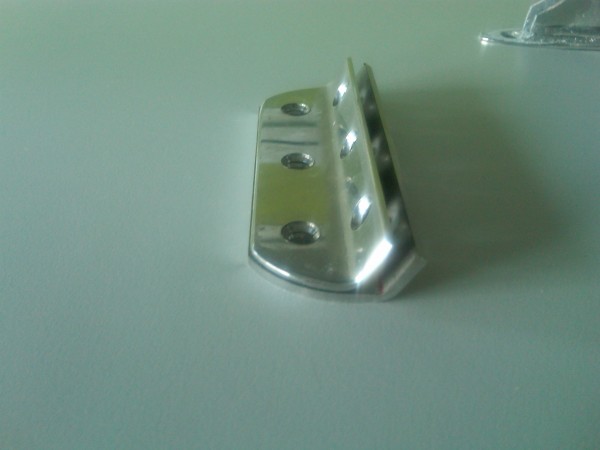
- Middle/Front part
We used 2 mm and 3 mm stainless steel sheets and I made several tries with it. 3mm parts are better for basis as they do not deform. The design is rather slim and we could have made the basis broader.
What frightens someone from doing it is, that it has several steps to be made (laser cutting, bending, crimping, welding, polishing drilling and mounting). Depending on how far away the professionals are to where you have to go to the longer it takes to have something produced.
So far to report about the prices encountered:
Stainless steel sheets .... 50 EUR
Laser cutting .............. 50 EUR
Crimping & bending ...... 50 EUR
Polishing and machining..100 EUR
The prices above do not include all travelling and time intensive after hours that I had to stay in workshops describing exactly what I want. It is very advisable to buy bigger sheets of stainless steel and have more parts cut than needed. The crimping and bending requires experience and I was lucky with the 2nd workshop, which make industrial and marine kitchens and had tools, experience and also intelligence not to destroy the material I brought them.
What is up next is the installation on board and the production of a wooden dummy shield, which will be used for a pattern. A UV resistant plexiglass will be bought and cut bigger than the pattern It will be inserted in an oven on the pattern and heated and bended untill it takes desired shape. A schoolmate of me who now builds boats will do this for me. He also needs to make these Plexiglass cooking procedures and advised me all that. There is also a more simple but unprofessional way which is made with a heatgun, where you bend on site during plexiglass installation. He says: You will not get the same results from this.
I'll keep you posted about the progress I made.